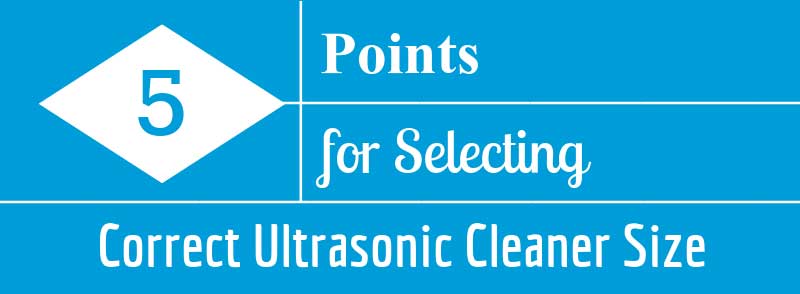
Selecting Ultrasonic Cleaner Size – 5 Key Points Consider
Ultrasonic parts cleaners are manufactured in a tremendous variety of sizes. By “size” we mean the dimensions and capacities of tanks in which ultrasonic parts cleaning is accomplished. For example the Elmasonic E Plus series is offered in 9 tank capacities from 0.25 to 7.5 gallons and the Select Series in 11 capacities from 0.7 to 23 gallons. Industrial-sized units such as SHIRACLEAN can hold 100 gallons or more. This post will help you select the correct ultrasonic parts cleaner size.
Five Points to Selecting your Ultrasonic Cleaner Size
- Parts you are cleaning
- Cleaning tank dimensions
- The importance of “working depth”
- The role of cleaning baskets
- Cleaning solution volume and service volume
1. What Parts are you Cleaning?
Ultrasonic parts cleaning has proved a very effective and economical way to remove all types of contaminants from nearly anything that can be safely immersed in an aqueous biodegradable cleaning solution.
Applications include cleaning and preserving vinyl records, dental instruments, heavy parts degreasing and aircraft engine components.
These and the thousands of other parts that benefit from ultrasonic cleaning have unlike dimensions in terms of length, width and depth. Which brings us to our second point:
2. Ultrasonic Cleaning Tank Dimensions
An important point to keep in mind when selecting your ultrasonic parts cleaner size is that parts must be fully immersed in the ultrasonic cleaning solution. Dipping one end in for a cleaning cycle then the other end is a no-go.
Fortunately off-the-shelf ultrasonic cleaners are manufactured in a variety of cleaning tank dimensions whether you are cleaning electronics and printed circuit boards or rifles. Custom-designs can be fabricated to accommodate large or oddly shaped parts.
A related point to keep in mind regarding the dimensions of your cleaning tank is that parts being cleaned should not be bunched together. Ideally they will be separated from each other. This both improves cleaning results and helps avoid damage when parts vibrate against each other due to ultrasonic action.
Which brings us to our third point:
3. The Importance of “Working Depth”
So, what the heck is working depth?
Ultrasonic cleaner baskets (described next) are designed to suspend products being cleaned at an ideal distance from the tank bottom. This maximizes the efficiency of the cleaning process. Without going into too much detail ultrasonic transducers are bonded to the underside of the tank bottom, causing it t vibrate, thus creating the cavitation bubbles that do the cleaning.
As with cleaning basket length and width being somewhat less than tank length and width, so too the bottom of the cleaning basket must be above the tank bottom.
Hence the term working depth. It is the distance between the bottom of the basket and the surface of the cleaning solution when the tank is filled to the proper working capacity.
From this one might surmise that to select the correct ultrasonic parts cleaner size based on what you are cleaning an early point to determine is the working depth of the equipment. Perhaps a case can be made that the working depth point should be number one in the selection criteria.
But you got this far in the post, so the point has been made.
We invite you to check out our short video on ultrasonic cleaner size.
4. The Role of Cleaning Baskets
Most ultrasonic parts cleaning cycles are accomplished in baskets* that allow parts to be easily immersed in and removed from the cleaning bath. They are essential because they keep parts from contact with the bottom of the cleaning tank where vibration will eventually wear holes in the tank, rending it unfit for further service.
What is important here is cleaning basket dimensions are smaller than cleaning tank dimensions. This allows easy placing and removing baskets using handles that rest over the side of the tank.
It is obvious then, when you select the size of your ultrasonic cleaner you take into full account the cleaning basket dimensions. Makes sense, right?
This information should be readily available from your ultrasonic parts cleaner tank supplier. The correct basket size will allow you to accommodate the dimensions of the parts you are cleaning. Keep in mind that they should not be stacked in the basket for reasons noted above.
5. Ultrasonic Cleaner Solution Volume and Service Volume
Last on our list re ultrasonic cleaner size is what is called displacement. You experience this when you add ice cubes to a glass filled with water. The same applies to ultrasonic parts cleaners. And here’s why:
Ultrasonic cleaners have a maximum solution volume and service solution volume. These statistics are provided in product detail sheets and user manuals. For purposes of discussion we define maximum volume as the amount of cleaning solution needed to fill the tank to its capacity – generally the fill line or other designation indicated in the operations manual.
The service volume is the amount of solution needed to accommodate displacement by parts being cleaned while allowing full immersion.
We use as examples two Elma x-tra ST industrial ultrasonic cleaners. For the x-tra ST 300 the service volume is 5.8 gallons and the maximum volume is 7.9 gallons. For the x-tra ST 2500 the service volume is 57 gallons and the maximum volume is 67 gallons.
Ultrasonic Cleaner Solution Volume Take-Away
Neither more nor less cleaning solution is better. Ultrasonic parts cleaners are designed to operate with a designed amount of cleaning solution. Overfilling the tank does not improve efficiency; under filling the tank does not intensify cleaning but instead can damage the tank. This, by the way, is why the service volume statistic is provided. It allows solution mixing, degassing and heating when baskets are empty.
The take-away? Account for displacement when calculating the amount of cleaning solution you need to do the job and take into account the recommended service volume provided by the equipment manufacturer.
Not Sure About Which Ultrasonic Cleaner Size Will Work for You?
Call or chat with the experts at Tovatech. We’ll provide unbiased information and support to ensure you purchase the correct size cleaner for your needs.